Ultrasonic Welder
High quality Ultrasonic Welding Supplies and Accessories
Lower prices on equipment and electrodes than other manufacturers
Shorter lead time, especially on electrodes
Free test welds and unparalleled customer support
How We Can Help You
Advanced Integrated Technologies ( AIT ) is a welding equipment and technical support provider for Nippon Avionics ( Avio ) brand of ultrasonic welders and accessories. We can evaluate your product samples, provide free test welds, and accurately specify which equipment is best for your application. We can then provide the equipment you need at an economical price, and assist with any technical issues you encounter setting up your welding process. Submit a contact form or call us today to request assistance with your next project.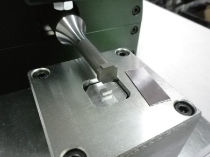
Introduction to Ultrasonic Welding
Principles of Ultrasonic Metal Joining
Unlike resistance welding, ultrasonic welder horn oscillator vibration removes oxide film on the metal surface and scatters surface layer impurities in order to create a state of solid-phase welding by bonding metal atoms.
Advantages
- Reduces damage and provides efficient energy use because of low welding temperatures (less than approx. 50% of the melting point)
- Suitable for connection of thin metal foil such as aluminum foil or thin copper foil. Also suitable for connection of copper wires.
- Reduces electrical resistance and provides joints with good electrical conductivity
- No special surface treatment required
- No consumables such as solder are required. Eco-Friendly while reducing costs
- Space-saving, easy to introduce automation
- Permits dissimilar metal joints, e.g., joining aluminum to copper
AVIO Ultrasonic Welders
- Ultrasonic Welders use Ultrasonic Energy to perform various bonding & cutting functions such as resin welding, resin seat cutting, resin cutting, and metal joining. The basic components of Ultrasonic Welding Systems consist of an Ultrasonic Oscillator Unit and a Welder Main Unit (Press).
- Products offered include a wide range of output models from a compact 40W unit to the world’s highest in class 8,000W unit to meet customer needs.
These products are manufactured by Nippon Future Co. Ltd. (a wholly-owned subsidiary of Nippon Avionics Co., Ltd.).
Features of Ultrasonic Welding
- Fast welding - For most applications, welding times are short allowing increased production
- Stable production - Setting conditions may be stored for future use ensuring consistent welds among production cycles
- Quiet performance - Non-audible frequency range is used for most products
- Air-tight seals – Selecting proper horns for each product accomplishes an air-tight weld
- Environmentally friendly - No adhesive chemicals are used during the manufacturing process that compromise security and recyclability
- Saves money - Shorter weld times significantly reduces manufacturing cost
Wide Selection of Ultrasonic Horns
Ultrasonic horns incorporate a half-wavelength resonator cavity which efficiently transmits vibration energy. Horn materials include aluminum alloy, titanium alloy, and die steel depending on the welding purpose.
We offer horns that best suit your particular work. We also design and manufacture clamping jigs.
Applications of Ultrasonic Welding
Examples of Ultrasonically Welded Parts
Maximum Output 8,000W – World's Highest Performance in Its Class!
Includes Color LCD Display and Simple-to-Use Touch Panel
W5000 series ultrasonic plastic welders allow control of welding parameters (welding time, welding displacement, welding energy, & welding data output). A color LCD touch screen front panel provides user friendly and intuitive operation.
Welding parameter data used for controlling can be output to a network environment (LAN) or saved to a USB storage device during operation. This easily accessed parameter data history is valuable for quality control.
Color LCD display of main weld parameter waveforms is beneficial for better on-site management and analysis of the welding process.
Wide Range of Welding Management Functions
•Welding energy control and management – Maintains welding energy constant and monitors the upper and lower limits of the weld head displacement
•Welding process control and management - Holds and monitors the melting depth (DEPTH) and finished dimensions(HEIGHT)
•Management and recording of set up & welding data – Records and timestamps each welding parameter. Supports USB storage devices and connection to a network environment (LAN).
•Control and manage welding time - Delay, Oscillation period, Retention time (cooling time)
•Display of power - Displays the peak power reached during welding
•Display and record welding waveform - Frequency, air pressure, applied current, displacement of welding head, actual applied pressure and energy can be displayed and recorded
•Other Functions
• Spherical seat parallelism adjustment
• Frequency check
• 2-step pressure
• After burst
• Load cell pressure measurement and management
• 1 μm resolution welding management
• Electro-pneumatic regulator pressure control
Ultrasonic Welder W5000 Series - Large Type
- A rigid press structure for welding large items
- Provides welds using super-sized horns
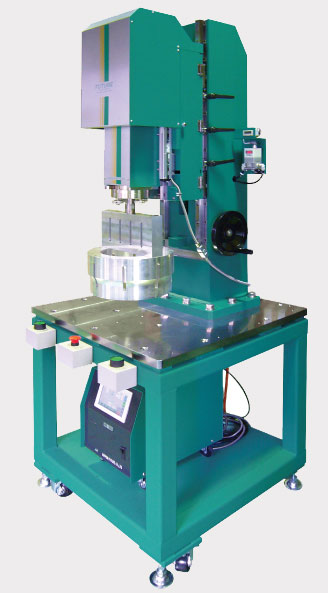
W5000 Series Ultrasonic Welders | ||||||||
W5040 | W5050 | W5070 | W5080 | W5085 | W5095 | W5155 | W5185 | |
Output Power | 1200W | 1600W | 2000W | 2400W | 2400W | 3000W | 5000W | 8000W |
Frequency | 20kHz | 15kHz | ||||||
Power Source | 3Φ AC200 V ± 5% 50/60Hz | |||||||
Oscillation Method | Frequency Automatic Tracking System (ATHMOS) | |||||||
Oscillator | ||||||||
Adjustment | Variable (0-100%, 1% step) | |||||||
Soft Start | Variable (40-200ms) | |||||||
Operation Type | Color LCD Touch Panel | |||||||
Welding Management System | Timer/Depth/Height/Energy mode,Waveform parameter display, Welding condition data recording (USB memory, LAN environment connection) | |||||||
Dimension WxDxH (mm) | 295x550x200 | 325x580x200 | 325x580x385 | |||||
Weight | ~10kg | ~13kg | ~16kg | ~30kg | ||||
Main Unit of Welder | ||||||||
Pressure Method | Air Cylinder (Electro-Pneumatic Regulator and Load Cell Equipped) | |||||||
Minimum Pressure | 120N | 170N | ||||||
Maximum Pressure | 1500N | 2500N | 5000N | 7000N | ||||
Welding Control Method | Linear Scale (0.001 mm res) | |||||||
Parallelism Adjustment | Spherical Seat-Style Support Flange | |||||||
Compressed Air Supply Required | Clean Air (0.06-0.5 MPa) | |||||||
Head Stroke | 315mm | Custom-designed | ||||||
Horn Stroke | 70mm (dia. 63mm Air Cylinder | 95mm (dia. 80mm Air Cylinder | Custom-Designed | |||||
Dimension WxDxH (mm) | 320x550x1215 | 380x610x1335 | Custom-Designed | |||||
Weight | ~52kg | ~88kg | Custom-Designed |
Basic Desktop Model of Ultrasonic Plastic Welder with Small-Footprint
Operation / setup iseasy. Changing horn height will not change the oscillator timing as the weld head is equipped with a pressure trigger. No adjustment required.
Standard equipment on this product includes: Frequency Monitor, Amplitude Adjustment mechanism and an External Ultrasonic Output

Oscillator Panel
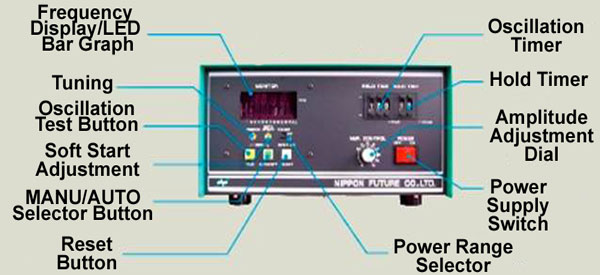
- Easy-to-see display of 12-step power switching.
- Work piece stresses are reduced by adjusting oscillator startingpoint (Adjustable soft-start)
- Oscillator amplitude is continuously variable between 0-100% toeasily select the optimum weld condition.
Automatic Welding Process Controller
•Vibrator has a casing
•Horn spherical seat leveling adjustment function is also available.
Ultrasonic Welder W3000 Series - Large Type
• A rigid press structure for welding large items
• Provides wide area welds using super-sized horns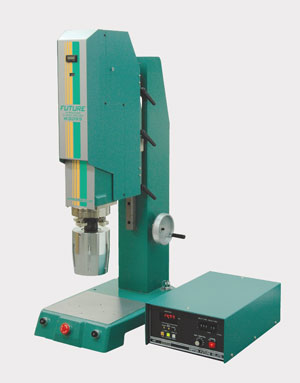
W3000 Series Ultrasonic Welders | |||||||||
W3040 | W3050 | W3070 | W3080 | W3085 | W3095 | W3155 | W3185 |
||
Output Power | 1200W | 1600W | 2000W | 2400W | 2400W | 3000W | 5000W | 8000W | |
Frequency | 20kHz | 15kHz | |||||||
Power Source | 3Φ AC200 V ± 5% 50/60Hz | ||||||||
Oscillation Method | Frequency Automatic Tracking System (ATHMOS) | ||||||||
Oscillator | |||||||||
Amplitude Adjustment | Variable (0-100%, 1% step) | ||||||||
Soft Start | Variable (40-200ms) | ||||||||
Dimension WxDxH (mm) | 295x500x180 | 325x500x180 | 325x500x385 | ||||||
Weight | ~10kg | ~12kg | ~15kg | ~30kg | |||||
Main Unit of Welder | |||||||||
Pressure Method | Air Cylinder | ||||||||
Minimum Pressure | 120N | 170N | |||||||
Maximum Pressure | 1500N | 2500N | 5000N | 7000N |
|||||
Parallelism | Spherical Seat-Style Support Flange | ||||||||
Compressed Air Supply Required | Clean Air (0.06-0.5 MPa) | ||||||||
Head Stroke | 315mm | Custom-Designed | |||||||
Horn Stroke | 70mm (dia. 63mm Air Cylinder) | 95mm (dia. 80mm Air Cylinder) | Custom-Designed | ||||||
Dimension WxDxH (mm) | 320x550x1215 | 380x610x1335 | Custom-Designed | ||||||
Weight | ~52kg | ~88kg | Custom-Designed |
Ultrasonic Hand Welder W2005-28/40

- Hand-held 250W ultrasonic welder•Wide range of applications from prototype to mass production
Ultrasonic Spot Welder W1002-60
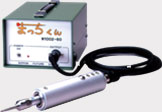
- Compact and lightweight ultrasonic spot welder
- Ideal for basting before sewing, small boss ratio caulking, and riveting.
Ultrasonic Small Welder Models W3011 - W3015
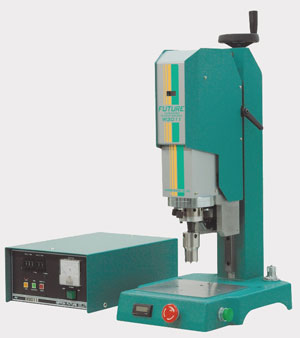
- Compact ultrasonic welder 500W - 800W
- Units for automation are also available.
Ultrasonic Vibrator Unit
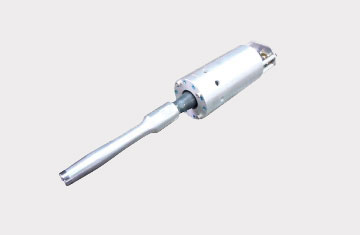
- Serves a wide range of applications when used in automation.
Compact Welder Series | |||||||
W2005 | W1002 | W3011 | W3012 | W3013 | W3014 | W3015 | |
Output Power | 250W | 40W | 500W | 800W | 500W | ||
Frequency | 28kHz. 40kHz | 60kHz | 20kHz, 27kHz, 28kHz, 39kHz, 50kHz | 27kHz, 39KHz | 20kHz, 27kHz, 28kHz, 39kHz, 50kHz | ||
Power Source | AC100V+/- 5% 50/60 Hz | 1 Φ AC200 V | AC100V+/- 5% 50/60 Hz | ||||
Oscillator | |||||||
Amplitude Adjustment | 0-100% with External Variable Transformer | 0-100% with External Variable Transformer | 50-100% (5 Steps) | 0-100% with External Variable Transformer | 0-100%(Continuously) | ||
Dimensions WxDxH (mm) | 164x242x105 | 123x170x88 | 254x365x146 | 254x415x146 | |||
Weight | ~2kg | ~1kg | ~6kg | ~7kg | |||
Main Unit of Welder | |||||||
Pressure Method | Hand Held | Air Cylinder | |||||
Maximum Pressure | 100N (10kgf) | 250N | |||||
Compressed Air Supply | - | - | Clean Air (0.06-0.5 MPa) | ||||
Horn Stroke | - | - | 75mm (dia. 25mm Air Cylinder) | ||||
Dimension | dia.36-52 x 275mm | dia. 31x159mm | 320x380x710 | ||||
Weight | ~450g | ~200g | ~30kg |
Ultrasonic Cutter W1003-40
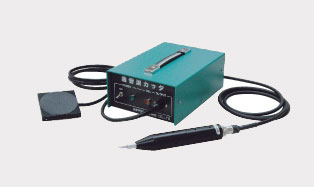
- Compact hand-held type ultrasonic cutter.
- Permits cutting of paper and resin, and "gate cutting".
Food Cutter
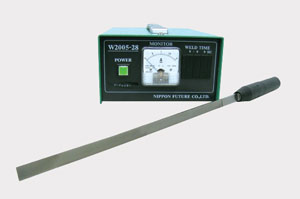
- Cleanly cut various confections such as cakes, sponge cakes, pies, candies, and various food types including vegetables, meat and fish.
- Solves unsightly appearance problems
- Eliminates dependence on skilled workers.
W1003 | |||
Output Power | 40W | ||
Frequency | 40kHz | ||
Power Source | AC100V+/- 5% 50/60 Hz | ||
Oscillator | |||
Dimension WxDxH (mm) | 39x200x186 | ||
Weight | ~1kg | ||
Main Unit of Welder | |||
Maximum Pressure | 50N (5kgf) | ||
Dimension | dia.24x200mm | ||
Weight | Approx.200g |
Ultrasonic Clear File Welder
(Ultrasonic Direct Welding)
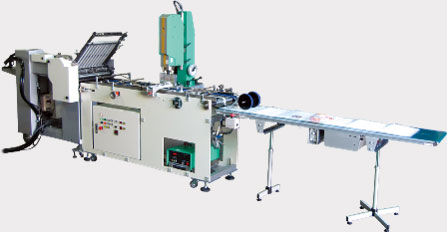
Welder with Stand
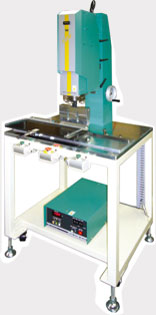
Soundproofing Unit
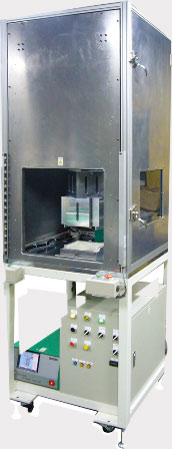
Simple Press Unit for HandyWelder
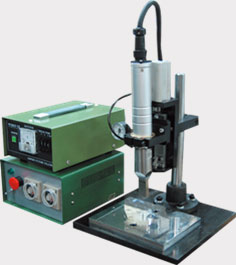
Multi-Type Ultrasonic Welder for Long Objects
(Ultrasonic Direct Welding)
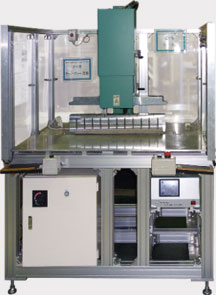
Multi-head Ultrasonic Welder
(Ultrasonic Transmit Welding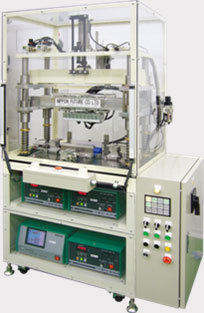
On Demand Sealer
(Ultrasonic Seam Welding)
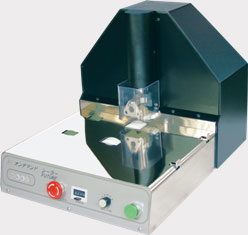
Mesh Ultrasonic Melt Cutting Equipment
(Ultrasonic Melt Cutting)
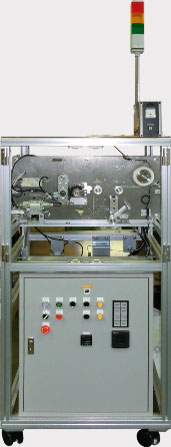
Multi-point Fusing Equipment for Automobiles
(Ultrasonic Boss Fusing)
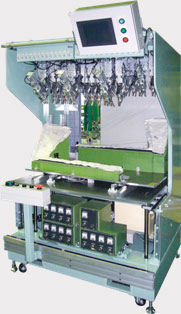
XYZ-Direct Robot-type Caulking Equipment (Ultrasonic Fusing /Insert)
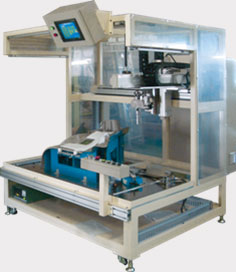
Bolt Nut Insert Equipment
(High-frequency Induction Heating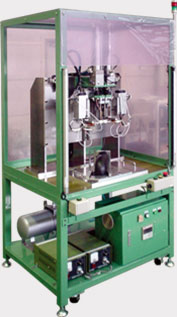
High-frequency Induction Heating Equipment
Metal Materials such as Screws or Nuts are easily Inserted into Molded Plastic Components!
Induction heating units incorporate high frequency generators for non-contact heating of metal using electromagnetic induction.
Induction heated metal screws and nuts can be easily and securely inserted into molded plastic components.
Unlike heater-method equipment, induction heating quickly heats both magnetic and non-magnetic materials. No pre-heating is required which contributes to reduced power consumption and prevents deterioration of metal parts.
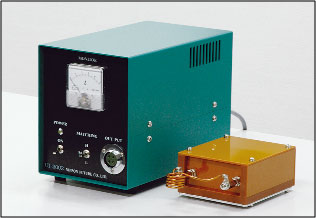
Various Induction Coils
We offer a wide variety of coils to suit your applications.
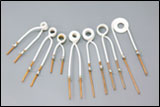
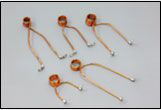
Induction Insert samples
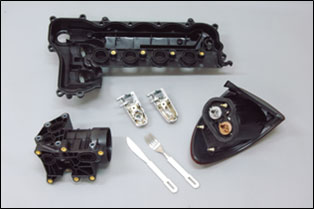