Hot Bar Soldering Equipment
Temperature Feedback Prevents Cobwebbing of Plastic!
Hand Piece Type
NCU-10U/T/H
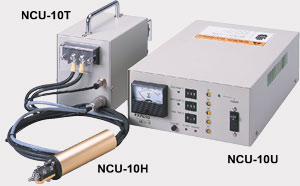
Heater Tip for NCU-10H
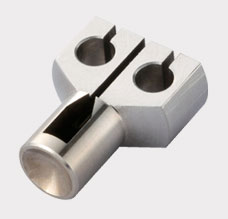
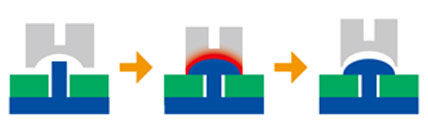
- Cooling Function: Because the process ends with the plastic solidified, stable fusing without cobwebbing can be achieved.
- Temperature Feedback Function: Temperature variation due to environmental change or passage of time is restrained. Stable Welding by temperature feedback (Plastic sputtering or cracking, as in the case of ultrasonic joining, will not occur)
- Easy to Transport Handy Type
- We can Propose the Most Suitable Heater Tip Based on Our Ample Experience: Heater tip material most suitable to the work material Flat type, multi-point simultaneous heater tip, special coating, etc.
- After Heat Helps Easy Separation of Plastic and the Heater Tip
Features | NCU-10U | Features | NCU-10T |
Heat Temperature |
Main: Room temp~499°C Idling: Room temp~299°C |
Rated Power | 150V |
Heat Time | 0.1-9.9sec(0.1sec/step) | Output Voltage | 1.75V, 2.5V, 3.5V |
Power Source | AC100V±10% 1Φ (Option:200, 230V) |
Dimensions (mm) | 100x150x120 |
Compressed Air | 0.4MPA or more | Weight | 3.4kg |
Dimensions (mm) | 200x302x90 | - | - |
Weight | 3.5kg | - | - |
The Best Seller Power Supply Unit Suitable for Soldering, Thermo-Compresion Bonding and Heat-Fusing!
Pulse Heat Power Supply
General Purpose Type
TCW-315
High Power Type
PHU-35
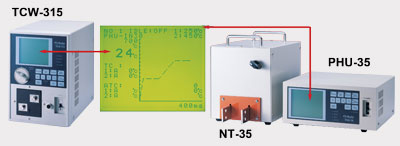
- High Reliability Joining: Becuause heating and cooling take place while the pressure is being applied, the work position will not be shifted during joining.
- Variable Temperature Profile: Because the heating is local and instantaneous, thermal impact to the peripheral components is restrained.
- High Reprodicibility: Digital PID control enables good reproducitbility of temperature and time. As a result, no skill of the operator is required.
- Pb Free Compatible: Pb free solder is accomodated by setting to high temperature and long heating time.
- User Interface: RS-232C&I/O is standard equipped, making the unit easy to be connected to external equipment such as incorporationg into an automated system.
- Ample Monitoring Functions: Temperature Monitoring: Upper and Lower limit (average peak), Profile Detection Error: Over-Heat, Thermocouple Disconnection, etc.
- Other Standard Functions: Number of stored settings: 15, Head vertical and cooling air control signal, Auxiliary thermocouple input, Counter function.
Features | TCW-315 | PHU-35 | NT-35 |
Heating Temp. |
Room temp~600°C/1°C step E, J-type Room temp~900°C K-type (Option) |
Room temp~600°C/1°C step E, J-type Room temp~900°C K-type (Option) |
- |
Heating Time | 000-999(x100ms, x10ms) | 000-999(x100ms, x10ms) | - |
Rating Power | 750VA | - | 3KVA |
Transformer | Built-In | - | - |
Tap Voltage | 0.88 V, 1.24 V, 1.75 V, 2.47 V, 3.5 V | - | 1.0V, 2.0V, 3.0V |
Power Source | 1Φ, AC200-230V±10%, (AC100-115V: option) | 1Φ, AC200-230V±10%, (AC100-115V: option) | - |
Dimensions(mm) |
200x320x283 | 278x250x120 | 200x270x220 |
Weight | 19.5kg | 7.4kg | 25kg |
Ultimate Pulse Heat Controller with Concurrency Control of Temperature and Displacement!
Pulse Heat Controller: Concurrency Control of Temperature and Displacement
TCW-DP100
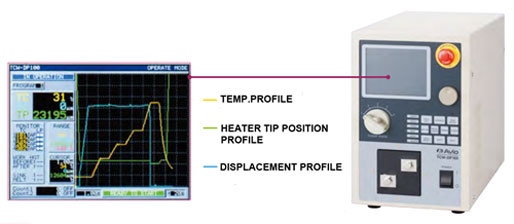
- High Precision Displacement Control: Overtravelling amount is controlled by feedback of displacement amount in 1μm resolution, and uniform melting amount can be realized.
- Wide Variety of Monitoring Functions (Temperature, Displacement)
- Digital Temperature Control: High speed and highly accurate temperature control is realized by the digital PID control method, making the unit suitable for fine wires and micro-miniature works.
- Release Function: After heating, the solder thickness between the works can be secured.
- Four Stage Heating: Various temperature profiles are realized to cope with the diversified applications
- Built-in Motor Control Function
- User Interface: RS-232C&I/O is standard equipped making the unit easy to interface with the external equipment such as the case of incorporating in an automated system.
Melting Amounts Control
Micro Co-axial Cable
- No Spread Wire (Damage Reduction)
- No Solder Bridge
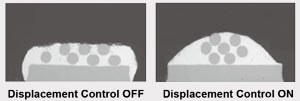
Joining Gap Control
Solar Panel Module
- Enhancement of Joining Strength
- Reduction of Residual Stress
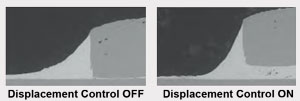
*Reflow head motor drive unitl Model NA-201P is required for use with Model TCW-DP100.*
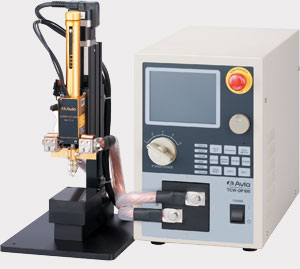
Features | TCW-DP100 |
---|---|
Heating Temperature |
Room temp~600°C in 1°C step, E type/ J type (option) Room temp~900°C, K type (option) |
Heating Time | 0.00-99.99 seconds |
Rated Capacity | 750 VA, 50% duty cycle |
Heating Steps | 4 Steps |
Monitor | Sink Amount, Temperature, Work Height |
Motor Resolution | 1 μm/pulse |
Displacement Resolution | 1μm |
Interface | RS-232C, I/O |
Transformer | Built-In |
Tap Voltage | 0.88 V, 1.24 V, 1.75 V, 2.47 V, 3.5 V |
Power Source | AC 200-240 V±10%, 1Φ, 50/60 Hz, 15 A |
Dimension (mm) | 220x400x320 |
Weight | 23kg |
FPC to PWB Reflow Soldering
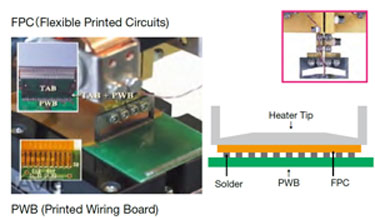
Insulation Wire to PWB Reflow Soldering
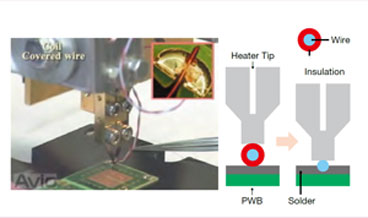
Co-Axial Cable and Grand Bar to Wire Reflow Soldering
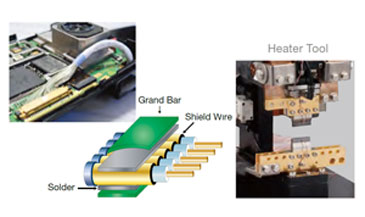
Solar Battery Module Assembly Reflow Soldering
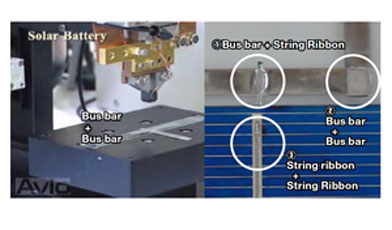
Camera Module Assembly Reflow Soldering
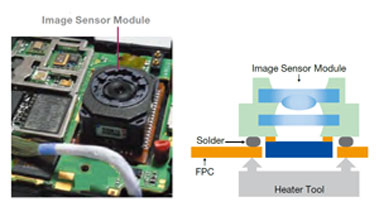
ACF (Glass to FPC)
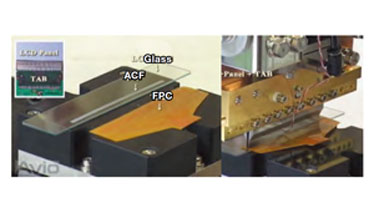
Plastic Parts Fabrication (PWB) Pulse Heat Fusing
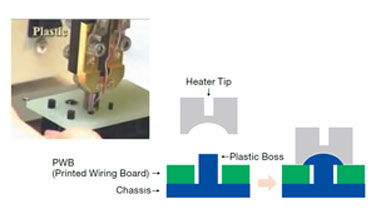
Plastic Parts Fabrication (Lens) Pulse Heat Fusing

Select a power supply with suitable welding capacity depending on the material or the shape of the object to be joined and the required quality level.
Reflow Head
Select a head having a force suitable to the object to be joined and suitable to the heater tip/heater tool to be used.
Outline of Pulse Heat Units
Pulse heat units from Nippon Avionics Co., Ltd. have been used over the years for various applications, including soldering in manufacturing of electronic equipment or electronic components, ACF bonding, plastic welding, and thermo-compression bonding.
In the recent years, improvement of both the function and the performance of mobile devices and other electronic equipment are being accelerated. While the parts are getting smaller and higher in performance, technology to mount parts in high density is becoming very important. Among other things, soldering, which is the key technology in parts manufacturing and assembly, is expected to cope with fine pattern and high reliability.
We are offering suitable micro-joining solutions in a timely manner to satisfy the needs of the customer in the manufacturing industry where technical innovation is remarkable.
What is Pulse Heat?
Pulse heat units are equipment used for soldering of electric components or welding of plastic components. It consists of a reflow head, which holds down the component and applies the force, and a pulse heat power supply, which flows the electic current.
Pulse heat is an instantaneous heating method whereby heating is effected only when melting the solder or the plastic. Solder or plastic is melted by the resistance heat generated by flowing electric current to a heater tip/ heater tool made of metal. Once the material is melted, electric current is stopped and cooled.
Because the object is held down with pressure until it is solidified, there is no lifting or shifting of parts, and, as a result, highly reliable joining can be achieved.
Basic Configuration of a Pulse Heat Unit and Role of Each Part
- Pulse Heat Power Supply: Electric current is flown to the heater tip or heater tool.
- Reflow Head: The object to be joined is held down and force is applied. The applied force is adjusted by a spring.
- Heater Tip & Heater Tool: This is the part which becomes hot by resistance heating. The one with a relatively small area is called "heater tip" and a larger area is called "heater tool".
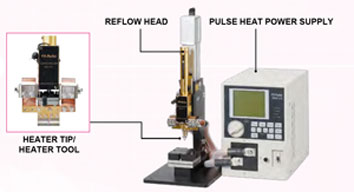
Pulse Heat Unit Model
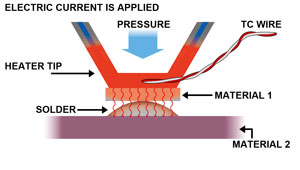
Temperature Profile
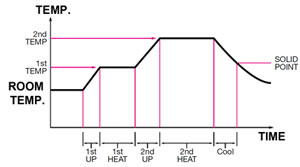
System Head Basic Configuration and Components | |||||
![]() |
![]() |
![]() |
![]() |
![]() |
![]() |
![]() |
![]() |
![]() |
![]() |
||
![]() |
![]() |
![]() |
![]() |